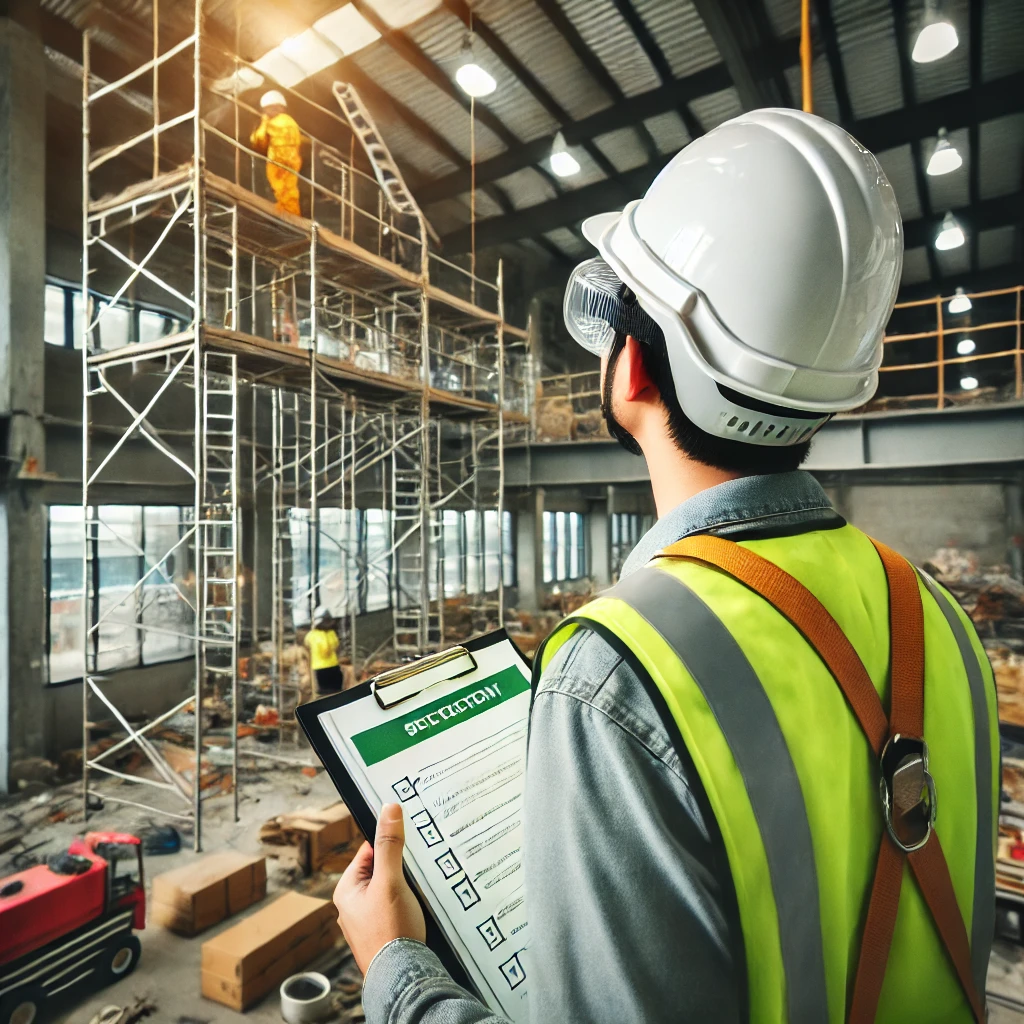
You’re walking your job site—boots on gravel, eyes on the day’s checklist—when a wrench crashes down from the scaffolding above. It misses your crew member by inches.
Close call? Definitely. Lucky? Absolutely. But luck isn’t a strategy.
This kind of near-miss happens more often than we like to admit. And if you’re not actively enforcing OSHA hard hat guidelines, you may be one small oversight away from tragedy—and major liability.
Let’s talk about turning that risk into resilience. Because compliance isn’t just about avoiding fines—it’s how you protect your people, your profits, and your reputation.
Why OSHA Hard Hat Guidelines Matter More Than You Think
When most business owners hear “OSHA,” they picture inspections, citations, and paperwork. But OSHA’s hard hat regulations are more than red tape—they’re a practical blueprint for safety leadership.
Work-related head injuries—especially traumatic brain injuries—cost U.S. businesses billions annually in lost productivity, claims, and long-term disability. Skipping or skimming over something as simple as proper headgear isn’t just an oversight—it’s an exposure.
What OSHA Actually Requires: No Guesswork
OSHA’s hard hat rules are clear and specific. They’re designed to make leadership easier—not harder.
1. When Are Hard Hats Required?
Per OSHA Standard 1910.135, protective helmets must be worn when:
- There’s a risk of head injury from impact, falling or flying objects
- There’s potential for electric shock or burns
If your team lifts, builds, wires, maintains, or trims—this applies to you.
2. Types of Hard Hats (Choose the Right One)
- Type I: Top-only impact protection
- Type II: Top and side impact protection
- Class G (General): Electrical protection up to 2,200 volts
- Class E (Electrical): Electrical protection up to 20,000 volts
- Class C (Conductive): No electrical protection
Buying the right type for your work environment is where safety starts.
3. Fit, Condition, and Usage
Even the best-rated helmet won’t protect your team if it’s:
- Cracked or UV-damaged
- Missing the suspension system
- Worn backward (unless rated for it)
- Modified with non-compliant attachments
Hard hats must be inspected before each use and replaced at the first sign of wear or damage.
The Hidden Cost of Non-Compliance
Skipping OSHA standards doesn’t just lead to citations—it can lead to:
- Severe injuries or long-term disability
- Six-figure lawsuits and rising insurance premiums
- Operational shutdowns and project delays
- Lost trust among clients, workers, and inspectors
When prevention costs so little, why gamble with something that could cost everything?
Case Study: A $250,000 Mistake
A Midwestern manufacturing firm was recently fined $250,000 after a worker was hit by a falling pipe. The employee’s hard hat was from an unverified supplier—sun-faded, unapproved, and never inspected.
Yes, the company had a checklist. But no one was actively enforcing the policy.
Safety on paper isn’t enough. What matters is what happens in real time.
Why Compliance Is a Business Advantage
OSHA alignment isn’t just about avoiding penalties—it can improve your bottom line. Here’s how:
- Fewer claims = lower premiums
- Proactive culture = stronger retention
- Well-documented safety = stronger bids
- Fewer injuries = less downtime
Safety builds confidence, and confident businesses earn more contracts, retain more talent, and operate with fewer surprises.
5 Steps to Build a Compliant Hard Hat Program
Step 1: Walk Your Site for Hazards
Identify every area with potential head injury risks—don’t assume.
Step 2: Choose the Right Hard Hats
Buy from certified vendors. Match Type and Class to actual jobsite conditions.
Step 3: Train Your Team (and Retrain)
Make sure everyone knows how and when to wear PPE—and that non-compliance has consequences.
Step 4: Create a Routine Inspection Schedule
Inspect, document, and replace regularly. Make someone accountable.
Step 5: Keep Records
Training logs, inspection checklists, and replacement records are your best defense in an OSHA audit.
→ Get a quote for coverage that aligns with your current risk level
Final Word: Compliance Is Protection You Can Measure
A compliant hard hat policy might seem like a small thing—until it’s not. One close call can change everything.
Make your jobsite a place where safety isn’t just assumed—it’s enforced, respected, and fully supported. And if you’re unsure how your current coverage protects you, we’re here to help.
→ Talk with an advisor who understands safety-first business strategies
—
FAQs: OSHA Hard Hat Guidelines
1. How often should hard hats be replaced?
Every 5 years (sooner if damaged). Internal suspension systems should be replaced annually.
2. Can workers wear winter caps or beanies under hard hats?
Only approved liners should be used. Unapproved layers can interfere with impact protection.
3. Do hard hats expire?
Yes. Most come with a manufacturer date. UV damage, heat, and regular use all contribute to breakdown.
4. Are stickers allowed?
Yes, if they don’t hide cracks or damage. Keep them at least ¾” from the brim.
5. What if someone refuses to wear a hard hat?
Non-compliance is your liability. Train thoroughly, document issues, and follow a firm disciplinary process.
Hashtags:
#OSHACompliance #WorkplaceSafety #HardHatStandards #InjuryPrevention #ConstructionRisk #SafetyLeadership #ComplianceMatters #BusinessInsuranceTips #SmartSiteManagement #ProtectYourCrew